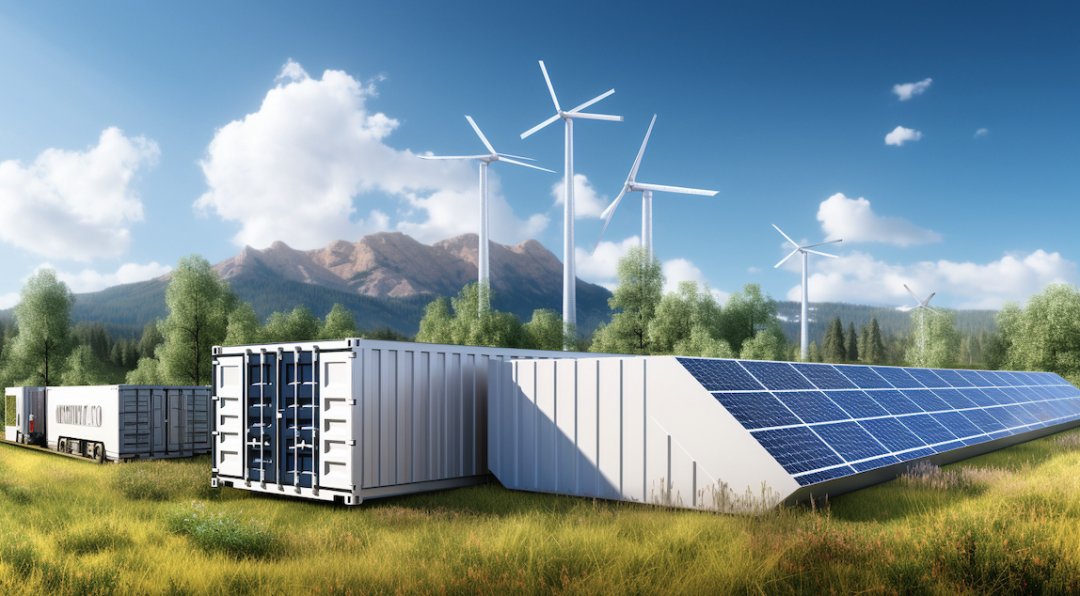
随着能源结构的快速调整,储能需求呈现高速增长趋势。
钒电池适用于大规模储能场景,如风电场、光伏电站的配套储能,以及电网调峰、备用电源等领域。
作为电化学储能领域中安全性较高的技术线路,钒电池正在成为大规模长时储能领域的优选方案。
据GuidehouseInsights的预测,到2031年全球钒电池的年装机量预计将升至32.8GWh。
本文对钒电池产业链核心环节和竞争格局进行梳理。
钒电池产业概述
钒电池因高安全性、长寿命和可扩展性等优势,成为长时储能的首选技术之一。
其电堆和电解液相对独立,储电量可以通过增大电堆功率和电解液来轻松提升,非常适合构建百兆瓦级储能电站。
在新型储能领域,钒电池成为锂离子电池储能的重要补充,与其他电池最主要的区别在于电解液的储存方式。
目前全钒液流电池的技术成熟度逐渐提高,产业链复杂度较高,涉及多个行业。其中核心环节是材料端和设备端。
上游:钒原料供给&电堆材料加工
钒电池产业链上游主要包括钒矿、原材料五氧化二钒、硫酸、碳材料、聚合物材料以及各类辅材。
钒矿及其加工业处于核心地位,是电解液原料五氧化二钒的主要来源。
国内钒矿布局厂商中,根据公开资料显示,龙佰集团在攀枝花的钒钛磁铁矿资源是中国最大钒钛磁铁矿,年产原矿1500万吨;明星电力持有四川奥深达资源投资开发公司100%股权,奥深达已获得四川甘孜和平武、陕西山阳、西藏江达、新疆且末等地的铁、锰、钒、银、铜、铅、锌等各类矿权共7宗;海亮股份收购的恒昊矿业拥有四座镍矿山,一座钒矿山、两座锰矿山和两座铜钼矿山。
电化学储能产业链图示:
材料端核心部件:电堆 电解液
电堆
电堆是全钒液流电池的核心部件之一,由多个单元电池串联而成,通过电化学反应将化学能转化为电能。
电堆的性能直接影响电池的输出功率和效率。
钒电池的电堆材料与氢燃料电堆相似度很高,主要包括电极、双极板、隔膜、密封件等几种关键材料。
当前全钒液流电池还没有大规模应用,因此几家代表性企业主要依靠自研自产或外协加工的方式生产电极材料,以供自用。代表厂商包括江油润生石墨毡、嘉兴纳科新材料等。
隔膜材料主要采用全氟质子交换膜,之后可能转向非氟传导膜。由于其制备工艺复杂,长期被杜邦、戈尔、旭硝子等美国和日本少数厂家占据,国内企业如东岳集团、江苏科润正在加速进行国产替代。东岳集团等企业已具备自主生产全氟磺酸树脂膜的能力,但液流电池用的高质量Nafion膜仍需进口且价格昂贵。
另一条路线是采用非氟离子传导膜,即非离子交换性隔膜,该技术是我国自主发展的方向,以中国科学院大连化学物理研究所为代表的科研团队已经取得了重要成果。上海电气、星辰新能、开封时代等厂商在该线路也有重点布局。
由于各厂家的选材和工艺不尽相同,电堆材料的成本及性能也存在差异性。
此外,现有电堆材料的技术和工艺尚有较大改进空间,相关研发工作仍在进行中,逐步实现国产替代。
电解液
电解液是钒电池的关键材料之一,直接影响钒电池的储电能力。
电解液储存了电池中的能量,并在电堆中通过氧化还原反应实现电能的转换,其配方和纯度对电池的性能有重要影响。
根据测算,储能时长为8小时的情况下,电解液的价值量占比53%,隔膜的价值量占比19%,石墨毡价值量占比5%,泵价值量占比4%,功率转换系统价值量占比12%。
电解液制造分为两个步骤:
1、核心前驱体的生产,即钒化学品(五氧化二钒、偏钒酸铵等),目前拥有相关技术和量产能力的基本为大型钒提炼及加工企业。
2、将前驱体转化为电解液。
电解液中核心成分的原料是五氧化二钒,国内钒资源产能相对集中,钒钛股份、攀钢钒钛、河钢股份、中核钛白、安宁股份等公司在钒钛资源综合使用和钒产品生产方面处于领先地位。此外,西部矿业拥有五氧化二钒的保有资源储量58.78万吨。
目前掌握钒电解液制造的全球龙头企业大连博融新材料公司全球市场占有率80%以上,已建成世界最大的首条大规模工业化钒电解液生产线。山东海化全资子公司山东海化氯碱树脂与液流储能能科技有限公司投资设立山东液流海材料科技有限公司,正在建设年产能36,000立方米的全钒液流储能电解液项目。丰山集团控股子公司丰山全诺在钒电池液流电解液方面进行了研发布局和技术储备,目前处在小试阶段。
全钒液流电池示意图:
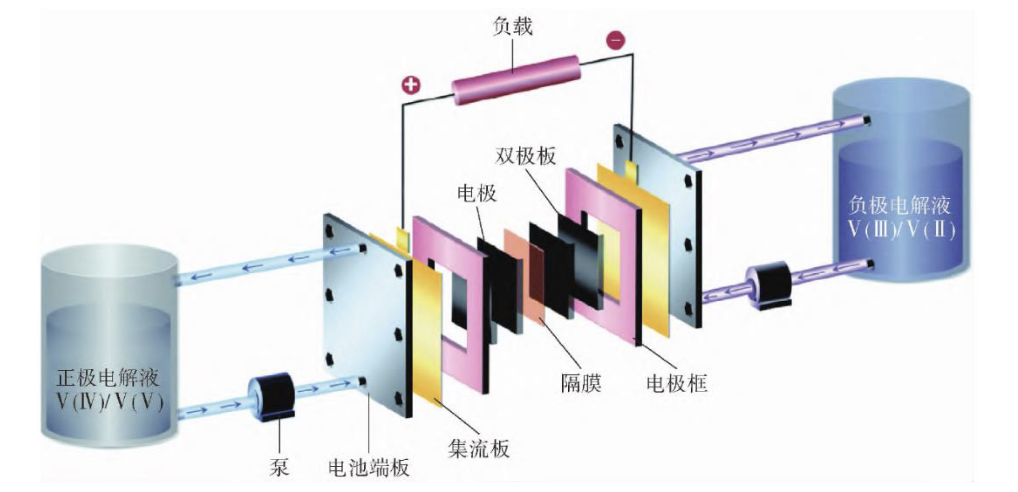
来源:中国有色冶金《全钒液流电池技术研究进展》
中游:电堆装配、控制系统等
全钒液流电堆的装配技术包括电堆装配、控制系统、其他设备和附件等,中游各环节技术壁垒较高,涉及各类耗材和电子元器件。
电堆装配
电堆端技术壁垒较高,具有技术积累和资本优势的行业龙头保持长期竞争力。
电堆装配的主要步骤包括单电池制备、电堆堆叠、密封处理和测试和调试等。
国内代表性企业有大连融科、北京普能、上海电气国轩新能源等;另有多家公司开展了相关布局,包括国网英大、西子洁能、易成新能、钒钛股份等。
控制系统
控制系统负责监控和管理电池的运行状态,确保电池的安全高效运行。
包括电力转换系统(PCS)、电池管理系统(BMS)、中央控制系统(CCS)等,所需硬件装置是电力电子行业的基本元件,可通过与相关企业合作定制生产。
PCS实现电池与电网之间的双向电力传递,包括双向逆变器、变压器、并网开关柜等设备,确保电池在充放电过程中的电能转换效率,主要厂商包括固德威,阳光电源、上能电气、科华数据等。
BMS是控制系统的核心,负责电池的监测、管理和保护。通过传感器采集电池的电压、电流、温度等数据,经过处理和分析后,输出控制信号,控制电池的充放电过程。比亚迪半导体、矽力杰、宁德时代等在该环节都有所布局。
整体来看,专门提供钒电池控制系统的企业较少,主要由相关企业自研自用或外协加工生产。
对于主要从事储能电控技术研发而尚未涉足钒电池的企业,未来较容易转型,为钒电池的控制系统提供解决方案服务,主要厂商如固德威等。未来待市场需求放量,可能会有更多的电控企业转型入场。
下游:终端应用市场
钒电池产业链下游终端市政主要包括各类储能用户,包括发电侧、电网侧、用电侧。
我国钒液流电池已实现在智能电网、通信基站、偏远地区供电等项目中的应用。
早在2022年,国家能源局首次批准建设的国家级大型化学储能示范项目大连液流电池储能示范项目正式并网投运,项目的投产并网将加速推动液流电池的大规模应用。
目前已有镇海网源友好型风电场储能项目、国家电投海阳储能示范项目进入并网阶段,同时襄阳全钒液流电池集成电站等工程项目处于建设中。襄阳高新区100MW/500MWh全钒液流电池储能电站项目由湖北绿动中钒新能源有限公司投资建设,建成后预计将成为全国最大的全钒液流储能电站。
此外,新天绿能投资建设了河北丰宁东梁储能一期项目,该项目装机容量100MW,同时采用了全钒液流电池储能技术,储能容量为2MW/8MWH。
东方电气集团东方汽轮机有限公司自2010年便开始全面开展全钒液流电池的研究,拥有核心知识产权体系。已建成成都川开120kW/500kWh储能系统、东方汽轮机1MW光伏 120kW/240kWh全钒液流光储充综合能源示范区等多个应用示范项目。此外,在钒电池产业链上下游均有布局,包括电解液、电堆、系统集成等环节。
钒电池市场格局
整体竞争格局来看,我国的全钒液流电池研究和产业化世界领先,技术层面已经相对完备。国内多家科研机构和企业,如中国科学院大连化学物理研究所、大连融科储能技术发展有限公司等,在全钒液流电池的关键技术,如电极材料、电解液、电堆结构等方面取得了重要突破,部分技术已达到国际领先水平。
但产业化进程仍处于蓄力发展阶段。目前,国内全钒液流电池的产能正在逐步扩大,但尚未形成明显规模效应。
国内钒电池设备企业大致有两类:
一类是科研院所自研技术转化的初创企业,多为校企合作模式,以大连融科为代表。
另一类是通过吸收合并或控股方式,获得相应技术,再优化升级参与竞争,以北京普能为代表。
全钒液流电池整机制造企业包括武汉南瑞、上海电气、东方电气、伟力得能源、上海神力科技等,各自拥有核心技术,普遍研发时间超过10年。
当前阻碍液流电池大规模商用的内因包括:性能单一导致应用场景局限,初始成本过高,导致经济性不足,外因是下游需求还未完成打开。
钒电池的初始投资成本还有较大下降空间,主要降本途径是降低可变成本(廉价材料替代,缩短制造流程等)、摊薄固定成本(增大功率密度,提高储能时长等)。
未来全钒液流电池的发展方向主要在于提升电池性能以拓展应用场景,以及降低系统的初始投资成本。在全钒液流电池产业化加速发展的过程中,产业链环节中电池端和材料端有望迎来机遇。